by tradesmeninsights | Jun 14, 2016 | Marketing Tips, Traditional Marketing
By John Sonnhalter, Rainmaker Journeyman, Sonnhalter
Every year, Industrial Distribution magazine puts out their annual survey of distributor operations. Here are some highlights from the 69th version and my opinion as to where they should be spending their time and effort.
While the economy is their biggest concern, it’s one they have little control over. Truth be known, I don’t believe the industrial segment of the market ever got back to levels pre-2008. Sales and margins are down (show me a business that doesn’t have similar issues) and that’s a natural reaction when sales drop, you try to protect existing business and the easiest way of doing that is lowering prices. Distributors can sometimes be their own worst enemies. Sell value not price.
Here’s my view of what these distributors should be concerning themselves with:
- Specialize – if you’re a general line distributor, I wish you luck as you won’t be in business too much longer. If the only thing you have to sell is price and availability, the big guys are going to eat you alive. The cutting tool, power transmission and other specialized distributors who add value to the sale will and can be more competitive. If you have a cutting tool problem on a CNC machine, Grainger or Amazon aren’t going to be sending anyone out to help you solve the problem.
- Promote value-added relationship selling – they are the local guys and should be selling themselves as the guys who have your back (assuming you have value to add). If not, look for a buyer.
- E-Commerce – Get in or you won’t be long for the world. We live in front of a computer screen and the “I want it now” mentality that we find on the consumer side has trickled over to ours. Let’s face it, some people would like to place orders after hours and they would like to know if you have it available and can have it delivered the next day.
- Buying groups – If you’re not in one, get in one. They are the easiest way for you to stay price competitive, and many offer other services in the day-to-day operations.
If you like this post, you may want to read:
by tradesmeninsights | May 3, 2016 | Marketing Tips, Marketing Tools, Marketing Trends, Traditional Marketing
By John Sonnhalter, Rainmaker Journeyman, Sonnhalter
We’ve had conversations here before about independent industrial distributors missing sales opportunities by not keeping up with the latest technology available.
I see that Industrial Distribution magazine is doing a webinar on this very subject on May 18th; you may want to sign up for it or suggest some of your independent distributors who are still lagging behind get in the game. Jon Eames from NH Bragg and Jack Templin from Affiliated Distributors will be contributors. Here’s what they will be covering:
Industrial customers are asking suppliers of all sizes to offer a highly functional e-commerce-enabled website. So how do smaller, independent distributorships take the first steps:
- Review ways independents can get in the game of e-commerce without breaking the bank.
- Hold true to their business objectives while developing an e-commerce strategy.
According to Forrester Consulting, a 2014 study shows that 52% of business buyers expect at least 50% of their purchases to be made online in 3 years’ time. This should be an eye opener for distribution, but some are ignoring the facts. The big boys like Grainger (40% of their sales are from the internet) and MSC Industrial (over 50% of their sales come from online) are certainly taking advantage. Shouldn’t that set the tone for the independents? Forrester forecasts that B-to-B e-commerce will exceed $1.1 trillion and comprise 12% of all B-to-B sales by 2020.
I’ve said in the past that for smaller industrial distributors to survive, they need to use the internet. They can’t count on the business model of contractors coming in at 7 in the morning or around lunch time to pick up what they need. Time is money, especially for them.
Industrial Distribution magazine recently released some research on The state of B2B e-commerce in Industrial Distribution. Here are some highlights:
- Independent distributors are slow-moving in implementing e-commerce programs.
- Technical challenges are making sites user-friendly, making it aesthetically appealing and staying ahead of the competition.
- Primary reasons of not engaging online was lack of demand, technical obstacles and lack of marketing/promotional resources.
Customer satisfaction and the customer experience are the key factors in developing an online presence. Ironically, that’s how the independent distributor built their business in the first place. Now they just need to transfer that to a different platform not only to keep existing business, but to grow additional revenue.
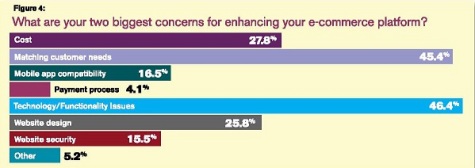
Source: Industrial Distribution
My worse fear is that the Amazons and the Alibabas of the world are going to make the independent extinct in a few years. I understand that the AD buying group has just instituted a new program to help members deal with some of these issues. It’s too early to tell if it’s making an impact, but at least they recognize the issue and are trying to help.
If you like this post, you may want to read:
What’s the future of small independent industrial distributors?
Are independent industrial distributors helping Amazon to succeed?
Distributor Strategy: What’s yours?
by tradesmeninsights | Mar 22, 2016 | Marketing Tips
By John Sonnhalter, Rainmaker Journeyman, Sonnhalter
I’ve addressed this issue in the past, and as time goes on, but I’m afraid the independent distributor may be following the way of the corner hardware store. Distributors need to step it up a notch!
Long before Grainger, Fastenal, Home Depot and the thing they call the Internet, the local industrial distributor was the backbone to local manufacturers and businesses. My, how things have changed over the past several decades.
I believe the small guy still has a chance to compete on a local level, but they need to change the way they do things. They need to know what their value proposition is, and most importantly, know their customers and what they want.

Source: Industrial Distribution magazine
If they can’t add value, then what’s the point? At the 2015 ISA Convention in Cleveland, one of the breakout sessions, “Looking Ahead at Distribution: The Future Impact of Size and Value Content 2015,” revealed some interesting issues. Mike Hockett, Associate Editor of Industrial Distribution magazine, did a good job summarizing both the results of the study, as well as the subsequent panel discussion.
Here are some highlights:
- Service sales represented only 5% of their total sales.
- Buying groups represented the best support.
- Manufacturers relied on small local distributors for customer loyalty and technical expertise.
It’s no surprise that cutting tools and abrasives remain the top two product categories that industrial distributors sell. Both require technical knowledge to support and troubleshoot problems. The question is, are the distributors going to charge for this expertise and are their customers going to be willing to pay for it?
So what do smaller industrial distributors need to do to stay in the game? Here are some thoughts:
- Embrace Technology – get an online sell site, integrated supply services and electronic billing for customers to order easily.
- Value Proposition – need to define so they can focus on the things that matter most and where they make their money.
- Buying Groups – need to get in one or more so you can stay competitive and make more money.
- Technical/Engineering Expertise – set yourself apart from the pack.
What others can you add to the list?
If you like this post, you might want to read:
Are Independent Distributors Helping Amazon Succeed?
Manufacturers: Tips on Getting More of Your Distributors Time.
by tradesmeninsights | Oct 28, 2015 | Marketing Tools, Marketing Trends, Traditional Marketing
By John Sonnhalter, Rainmaker Journeyman, Sonnhalter
We’ve had conversations here before about independent industrial distributors missing sales opportunities by not keeping up with the latest technology available.
According to Forrester Consulting, a 2014 study shows that 52% of business buyers expect at least 50% of their purchases to be made online in 3 years’ time. This should be an eye opener for distribution, but some are ignoring the facts. The big boys like Grainger (40% of their sales are from the internet) and MSC Industrial (over 50% of their sales come from online) are certainly taking advantage. Shouldn’t that set the tone for the independents? Forrester forecasts that B-to-B e-commerce will exceed $1.1 trillion and comprise 12% of all B-to-B sales by 2020.
I’ve said in the past that for smaller industrial distributors to survive, they need to use the internet. They can’t count on the business model of contractors coming in at 7 in the morning or around lunch time to pick up what they need. Time is money, especially for them.
Industrial Distribution magazine recently released some research on The state of B2B e-commerce in Industrial Distribution. Here are some highlights:
- Independent distributors are slow-moving in implementing e-commerce programs.
- Technical challenges are making sites user-friendly, making it aesthetically appealing and staying ahead of the competition.
- Primary reasons of not engaging online was lack of demand, technical obstacles and lack of marketing/promotional resources.
Customer satisfaction and the customer experience are the key factors in developing an online presence. Ironically, that’s how the independent distributor built their business in the first place. Now they just need to transfer that to a different platform, not only to keep existing business, but to grow additional revenue.

Source: Industrial Distribution
My worse fear is that the Amazons and the Alibabas of the world are going to make the independent extinct in a few years. I understand that the AD buying group has just instituted a new program to help members deal with some of these issues. It’s too early to tell if it’s making an impact, but at least they recognize the issue and are trying to help.
If you like this post, you may want to read:
What’s the future of small independent distributors?
Are independent industrial distributors helping Amazon to succeed?
Distributor Strategy: What’s yours?
Aesthetic issues (product descriptions, product images, graphics, logos) 22.1%
Cost 7.1%
Keeping pace with or staying ahead of competitors 18.6%
9
by tradesmeninsights | Jun 30, 2015 | Marketing Tips, Traditional Marketing
By John Sonnhalter, Rainmaker Journeyman at Sonnhalter
Distributors in general are their own worst enemies when it comes to the value they bring to the table and charging customers for it. As their customers are asking for more and are willing to pay less, the distributors’ margins are being reduced and they don’t know how to change the momentum.
If you’re a general line distributor, I wish you the best of luck as you are destined to go out of business if you continue to follow this path. Most distributors who have a specialty like cutting tools/abrasives, power transmissions, bearings, etc. have a distinct value to the proposition, but many aren’t taking advantage of it.
Traditional brick and mortar distributors can’t compete with online catalog sites on price, but what if there’s an on-site production problem? Over the years, I’ve been on several joint end-user calls where the distributor and manufacturer are going in to solve a production problem.
Long ago, the distributors just solved the problems and didn’t charge for it (by the way, it wasn’t usually the product the distributor sold them; it was how the customer was or was not using it correctly).
I recently read an article in Industrial Distribution by Bill Moore from SKF on how distributors can put a dollar sign on the valuable services they offer. Here are some highlights:
- Understand your value stream – Are you taking advantage of all the support your manufacturing partners are offering such as training or engineering assistance? All can contribute to a cash value at the customers.
- Understand the customers’ challenges – Instead of selling him cutting tools, find out what type of production issues they’re having using the tools. Help him solve that. Add value they can’t get somewhere else.
- Valuate your services – What do you bring to the table that they’d have to hire an outside consultant to do? What price can they put on not having to shut down a production line?
Bottom line is, take advantage of what your supplier partners have to offer. They can help you improve your value and add $ to your bottom line.